A2RL: How to effectively handle the autonomous race-car testing process
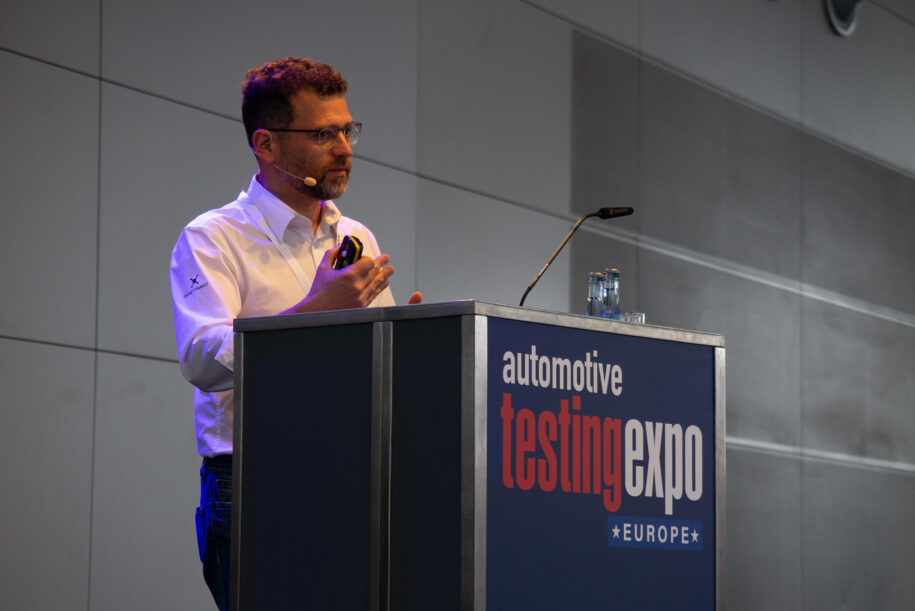
From May 20 to 22, 2025, Stuttgart hosted Automotive Testing Expo, the world’s leading event for testing, development, and validation technologies in the automotive sector. The exhibition brings together industry leaders and innovators shaping the future of vehicle engineering.
During the event, Claudio Annicchiarico, CEO of Meccanica 42, took the stage to share insights into one of today’s most ambitious autonomous driving initiatives: the Abu Dhabi Autonomous Racing League (A2RL). Launched by ASPIRE in April 2024, A2RL is a global competition designed to push the boundaries of AI-driven mobility. Based on Dallara Super Formula cars with no cockpit or human driver, the challenge lies in enabling autonomous systems to deliver performance, safety, and reliability at racing speeds.
Meccanica 42 played a key role in this project by supplying advanced actuators (Corner Brake Actuator, Pinion-type Steering Actuator) and a mid-level control unit (Body System Unit) for the autonomous driving systems. These components translate driving decisions and commands into real-time actions, controlling the engine, brakes, and steering system to ensure each race car performs at its best on the track.
During the session, Claudio illustrated how real-time tools, including both on-board devices and test rigs, were used to design, test, and verify the systems involved. These tools helped address challenges related to performance, safety, and fault handling in an autonomous racing context.
A2RL uses Dallara Super Formula Japan race cars modified for full autonomous operation.
The cars are equipped with:
1.External sensors to perceive the environment
2.Internal sensors to monitor vehicle dynamics
3.Actuators to control the car
4.A high-level pc, where teams upload their AI-based driving strategies.
The system architecture designed for 2024 was the following:
This setup allowed teams to develop the software while ensuring top-tier functional safety. With this configuration, the fastest autonomous lap time was just 10 seconds behind that of a professional driver.
In preparation for the 2025 season, the competition set new development targets:
Meccanica 42 deployed these targets at each level of the development cycle:
Vehicle level
System level
Focusing on brake-by-wire system and steer-by-wire system:
Component level
Once specifications were defined, validation began across three levels:
Component level
Vehicle Level
The same test benches were then integrated into a virtual vehicle setup combining the steering rig, brake rig, and a platform housing all actuators. This full test bench replicated the vehicle’s core systems, exchanging data with the virtual vehicle and receiving real-world physical inputs from the simulation.
This enabled:
Developing autonomous vehicles brings unique challenges, especially when it comes to on-track testing. Reducing real-world test kilometres is essential not only for safety and cost reasons, but also because time investment doesn’t always scale linearly with distance covered.
To address this, front-loading the validation process becomes crucial. Using the right tools from the early stages of development helps accelerate release timelines and reduce costly iterations.
A well-integrated toolchain supports scalability, allowing teams to efficiently manage increasing system complexity.
Finally, simulation and lab-based testing can converge when real-time test benches are connected to driving simulators, they create a powerful environment for vehicle-level validation, offering the realism of physical components with the flexibility of virtual testing.
For further discussion, below are more articles on the topic
For more information about our innovative solutions and how they can streamline your vehicle’s functions development, please contact us.
Don’t forget to follow us on LinkedIn, Instagram, and to subscribe to our newsletter to stay in the loop!