Driver-centric development leveraging remotized Hardware-in-the-Loop and dynamic driving simulators
HiL systems took center stage at the VI-grade Zero Prototypes Summit 2025 (13–15 May), where Claudio Annicchiarico from Meccanica 42 and Andrea Spicuglia from Stellantis, presented a talk titled “Driver-Centric Development Leveraging Remotized Hardware-in-the-Loop and Dynamic Driving Simulators”.
The session showcased how advanced real-time Hardware-in-the-Loop systems accelerate development by enabling early testing on real components, virtual calibration, and seamless integration with dynamic simulators.
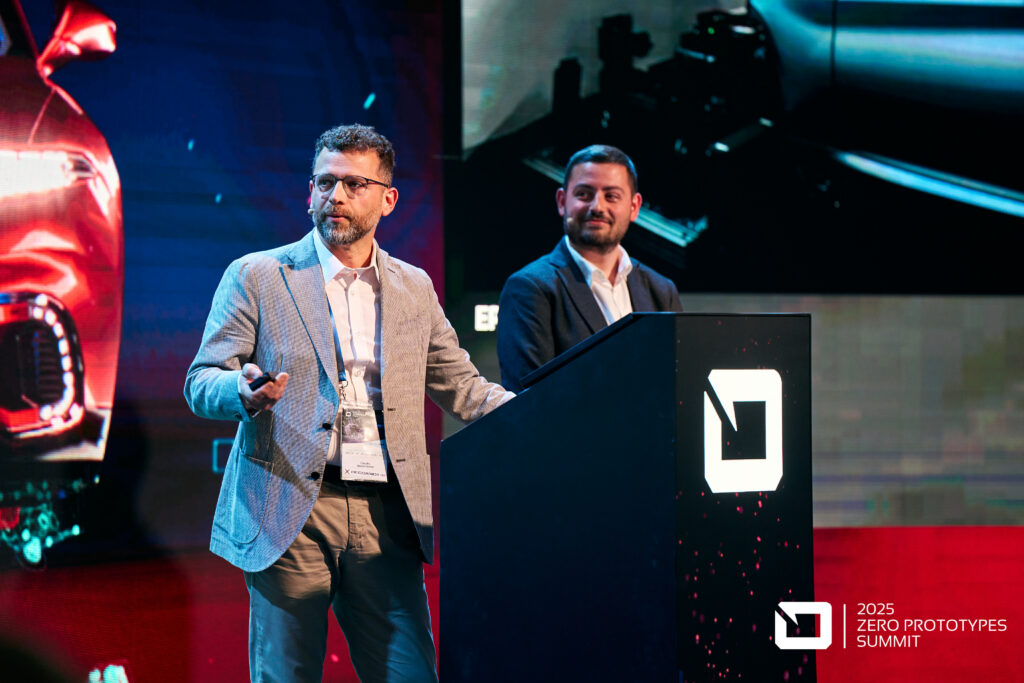
HiL and driving simulators as a development accelerator
In recent years, driving simulators have become increasingly central in the vehicle development process, supporting activities from concept design to final validation.
Among these, Hardware-in-the-Loop test benches are particularly valuable: by integrating real vehicle components into a simulation environment, engineers can debug functionalities, calibrate systems, and validate performance long before having a full prototype.
Beyond saving time and reducing costs, HiL benches enable virtual road release, functional safety assessments, and fault injection — all of which contribute to a more robust and efficient development workflow.
A HiL steering bench remotely connected to a dynamic simulator
Stellantis had already been using a Meccanica 42 steering test bench (EPSiL Gen 2) in a static simulator setup.
Later, they aimed to integrate it with a dynamic driving simulator (DiM). To meet this requirement, Meccanica 42 developed a remote integration approach that did not require any changes to the existing simulator.
This enabled engineers and drivers to interact with real hardware while immersed in dynamic, motion-based virtual scenarios, expanding the possibilities for calibration, validation, and driver-in-the-loop testing.
The system: real-time, modular, multi-simulator ready
The solution presented included two main systems, both enhanced for remote operation and full integration with one or more simulators:
EPSiL
Originally commissioned in 2019, EPSiL was upgraded with two crucial elements:
- A steering robot, allowing the steering rack to be actuated by a motor instead of a physical steering wheel.
- A steering motor cube, a dedicated frame that holds the steering robot and enables precise adjustment of the steering column’s position relative to the steering rack, replicating real-world mounting conditions.
This setup made it possible to calibrate key functionalities such as the EPS boost curve, damping characteristics, and ADAS steering behaviour, all within a real-time simulation loop.
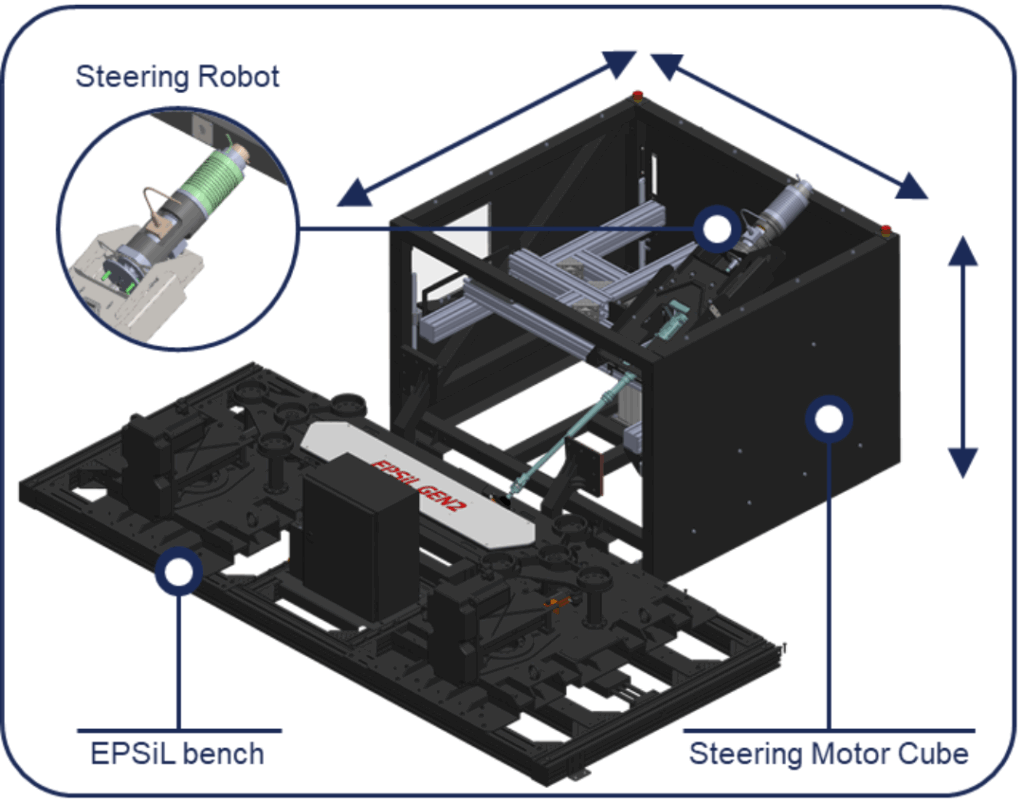
BrakeiL
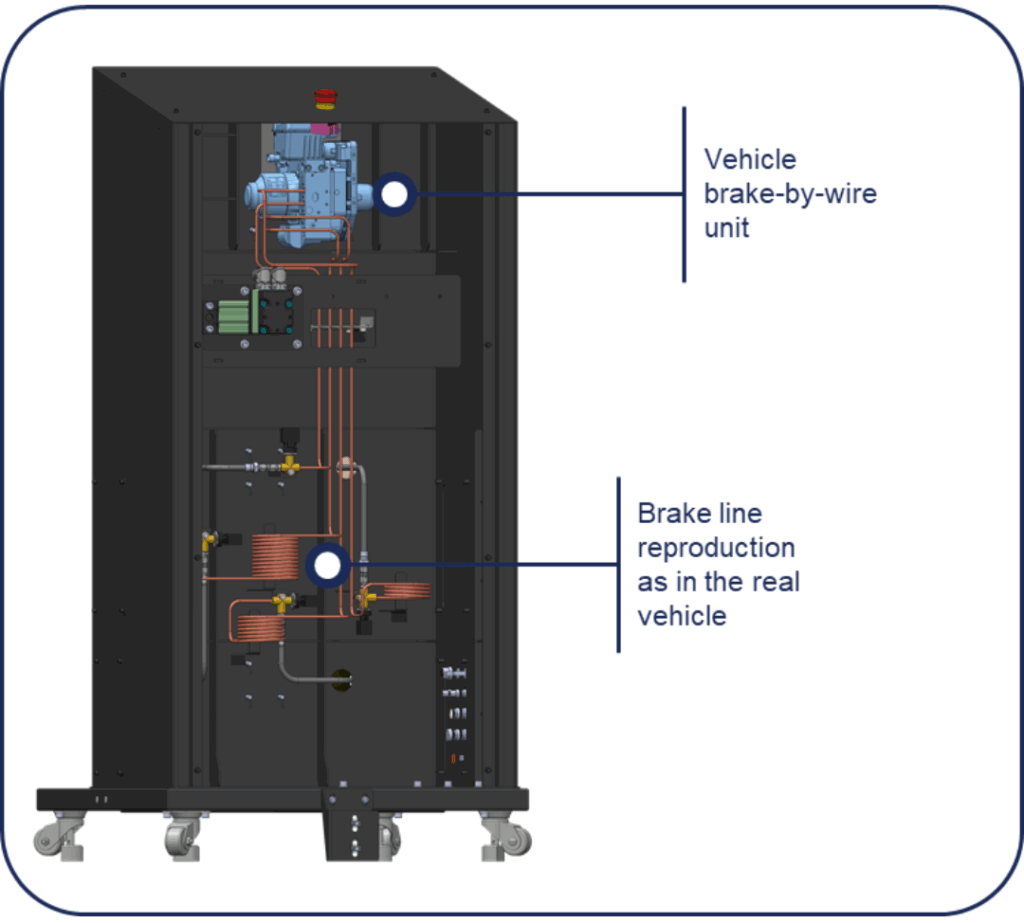
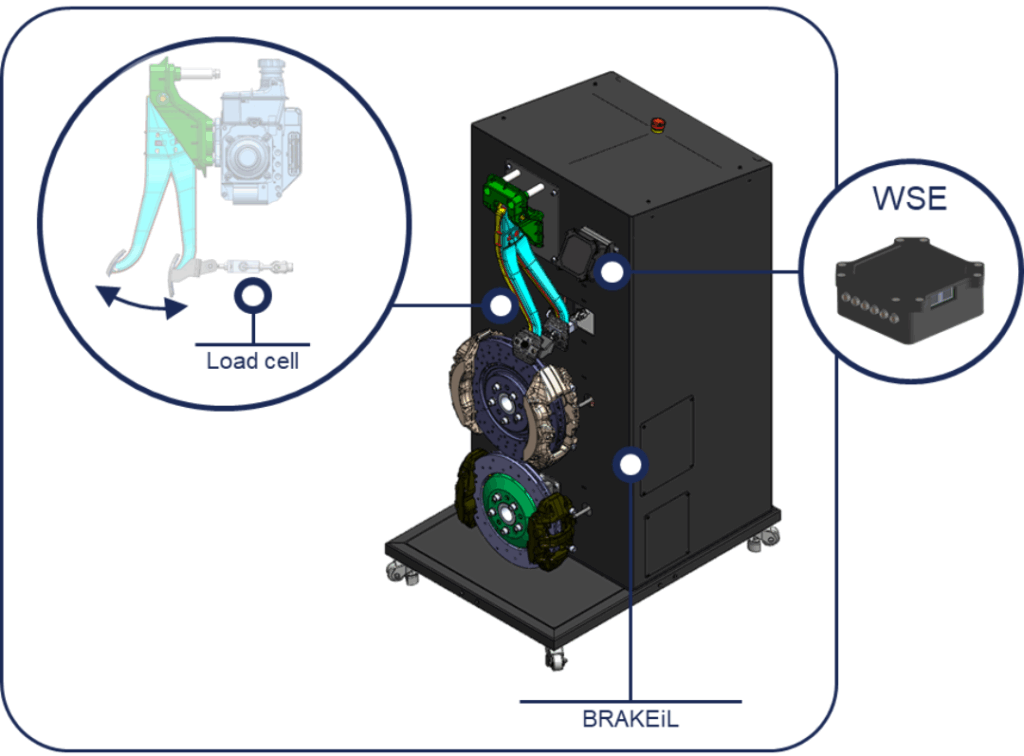
Meccanica 42’s braking test bench replicates the full braking architecture, including:
- Brake pedals
- ECU
- 4 calipers
- Linear actuator on brake pedal
- An equivalent hydraulic circuit with physically replicated brake lines, matching real vehicles in both length and stiffness.
On top of the bench, an ECU emulator (WSE) receives wheel speed signals from the simulator and converts them into raw sensor inputs, ensuring full signal chain integration.
A force actuator reproduces the pedal behaviour based on driver input in the simulator cockpit.
This architecture enables accurate calibration of:
- ABS and ESC
- Brake blending between hydraulic and regenerative systems
- ADAS braking functions
Both EPSiL and BrakeiL were designed with modularity and scalability in mind. The components can be used with different simulators (e.g., steering with one simulator, braking with another), or decoupled entirely for component-level testing.
The result: high realism, fast response, flexible testing
One of the key objectives of this project was maintaining real-time response with minimal latency between the simulator cockpit and the physical components.
Testing confirmed excellent tracking performance:
- The steering angle target vs. measured values showed near-perfect correspondence, even in fast step-and-release maneuvers.
- The pedal force vs. travel behaviour closely matched between HiL and cockpit, delivering a realistic driver feel.
Comparative data from on-road testing further confirmed the fidelity: experimental curves from the vehicle overlapped with those measured on the HiL bench, validating the realism of the setup both subjectively and objectively.
Conclusion: integrating virtual and physical, from concept to calibration
The work presented at ZPS 2025 demonstrated that remote HiL systems can effectively connect simulation and physical testing. By integrating real components into dynamic driving environments, engineers can validate systems earlier, tune them more precisely, and simulate critical scenarios in controlled conditions.
EPSiL and BrakeiL offer an example of how driver-centric development can be achieved without compromise — bringing together mechanical accuracy, real-time capability, and immersive simulation. This approach doesn’t aim to replace physical testing, but to enhance and accelerate it, empowering teams to design smarter, safer, and more efficient vehicles.
For more information about our innovative solutions and how they can streamline your vehicle’s functions development, please contact us.
Don’t forget to follow us on LinkedIn, Instagram, Facebook and to subscribe to our newsletter to stay in the loop!